Have you ever wondered how a delicate gold ring, silver pendant or brass bracelet goes from a sketch to a real object? In the past, jewelry manufacturing relied on skilled craftsmen to hand-carve wax models, which was time-consuming and costly. Now, CAD (computer-aided design) and CAM (computer-aided manufacturing) technologies make jewelry production more efficient and accurate, and even achieve complex structures that are difficult to complete with traditional craftsmanship.
For jewelry design manufacturers like Fulcol that specialize in custom jewelry, mastering CAD/CAM technology means faster response to customer needs, less material waste, and ensuring the accuracy of each product. CAD/CAM not only speeds up the design process, but also ensures high-precision manufacturing and reduces material waste. Whether it is personalized wedding rings, delicate pendants, or mass-produced fashion jewelry, these technologies can provide more flexible and efficient solutions.
Table of contents
- Basics of jewelry CAD modeling
- Basic knowledge of jewelry CAM processing
- Is CAM necessary?
- CAD and CAM in the jewelry industry: What is the difference?
- Application process steps of jewelry CAD and CAM in jewelry manufacturing
- Benefits of CAD and 3D rendering for jewelry business
- What is the difference between jewelry rendering and finished jewelry?
Basics of jewelry CAD modeling
What is CAD?
CAD (computer-aided design) is the process of creating jewelry models in a virtual three-dimensional environment using professional software. Compared with traditional hand-drawn sketches, CAD can achieve:
High precision and editability: Through precise parameter and dimension input, the model error can be controlled within ±0.01 mm, ensuring the accuracy of subsequent processing or printing.
Fast iteration: Easily adjust design details (such as gemstone setting holes, grain shape) without hand-drawing multiple sketches from scratch.
Data management: All design parameters are saved in digital file form, which is convenient for version control and team collaboration.
Recommended mainstream jewelry CAD software
Software | Applicable scenarios | Learning difficulty |
RhinoGold | Suitable for beginners, rich plug-ins | ⭐⭐ |
MatrixGold | Industry standard, supports complex designs | ⭐⭐⭐ |
ZBrush | Good at organic textures (such as animal and flower carvings) | ⭐⭐⭐⭐ |
Blender | Free, but the learning curve is steep | ⭐⭐⭐ |
The core steps of 3D modeling
- Sketch import: Scan the hand-drawn draft or draw the outline directly in the software.
- Basic modeling: Use NURBS (Non-Uniform Rational B-Spline) or polygon modeling to build the main body.
- Detailed engraving: Add textures, inlays, engravings, etc.
- Size calibration: Ensure that the inner diameter of the ring, chain width, etc. meet the actual wearing requirements.

Basic knowledge of jewelry CAM processing
What is CAM?
CAM (Computer-Aided Manufacturing) is the process of converting CAD design files into machine executable code (such as G-code) to drive CNC milling machines, laser cutting machines or 3D printing equipment for physical processing. The key links of CAM include:
- Toolpath planning
- Processing parameter (cutting speed, feed rate, tool compensation) setting
- Simulation verification and post-processing
Through CAM, the design can be efficiently reproduced in batches, significantly improving production consistency and accuracy.
Common CAM processing equipment and processes
Process type | Typical equipment | Application scenario |
Micro CNC milling | Roland MDX-540, DMG MORI CMX Mini | Prototyping wax model, metal blank preliminary processing |
Electrical discharge molding | Sodick, Mitsubishi EDMed | Complex hollowing, titanium alloy, difficult to process high hardness materials |
3D printing | Carbon, Formlabs | Resin wax model, plastic model, rapid prototyping (RP) |
Laser melting | EOS M 100, Renishaw | Metal powder direct printing (DMLS/SLM), suitable for complex casting molds |
Is CAM necessary?
Comparison of the advantages and disadvantages of traditional manual vs. CAM processing
Project | Traditional manual production | CAM processing |
Precision | Error ≈ ± 0.1–0.2 mm | Controllable error ± 0.01 mm |
Efficiency | Single piece production cycle 3–7 days | One-time programming can be used for batch processing, 1–3 hours for single piece |
Consistency | Large manual differences, difficult to reproduce details | Stable and consistent under digital instructions |
Cost | High labor cost, high unit cost at low batches | Programming cost is concentrated, but the cost of batch production has dropped significantly |
Creative flexibility | High, details can be adjusted at any time | Need to be reprogrammed and adjusted, high requirements for rapid iteration |
Which jewelry production links require CAM?
- Complex geometric structures (such as hollowing, micro-inlay)
- Batch production (reduce labor costs)
- High precision requirements (such as customized wedding rings)
Cost, efficiency and precision considerations
Initial investment: The purchase cost of high-precision CNC and EDM equipment ranges from tens of thousands to hundreds of thousands of US dollars. For small and medium-sized studios, you can choose to outsource CAM services or purchase imported desktop equipment.
Long-term benefits: According to industry experience, after the introduction of CAM, the development cycle of complex styles can be shortened by 30%-50%, and the unit cost of batch orders can be reduced by 20%-40%.
Therefore, if your business focuses on single product customization and the batch size is not large, you can flexibly adopt a combination of manual and digital processing. If you pursue high efficiency and standardization, CAM is almost a must-have option.

CAD and CAM in the jewelry industry: What is the difference?
When designing jewelry, many people tend to confuse the concepts of CAD and CAM. Simply put:
- CAD is the designer’s brush (responsible for creative design)
- CAM is the craftsman’s tool (responsible for physical production)
Functional positioning and work links
CAD mainly focuses on the “creativity and design” stage, focusing on the geometric shape, structural rationality and aesthetic expression of the model.
CAM focuses on the “production and manufacturing” stage, converting CAD data into physical entities, focusing on process feasibility, processing parameters and machine tool compatibility.
Output file format and connection method
Link | File format | Function |
CAD | .3dm, .prt, .jewmod, etc. | Save the original editable design |
Export | .STL, .OBJ | Triangular mesh model for CAM processing |
CAM | .NC, .Gcode | Machine-readable instructions for driving machine tools |
Team division of labor and collaboration process
- Designer (CAD): Complete the creative model and check the structural reliability.
- Process engineer (CAM): Generate processing strategy based on material and machine characteristics.
- Machine operator: Execute the processing program and monitor the processing quality.
- Quality inspection and post-processing: burr removal, polishing, coating or electroplating process.
Application process steps of jewelry CAD and CAM in jewelry manufacturing
Demand communication and concept confirmation
First, the designer and the customer or brand manager discuss the style intention, material selection, budget and delivery cycle in detail through face-to-face meetings, video calls or online collaboration platforms, and collect hand-drawn sketches or effect reference drawings. This stage clarifies the project positioning, determines the design scope and feasible processing technology, and provides a foundation for the subsequent digital process.
CAD 3D modeling
After confirming the concept, the designer uses professional software such as Rhino, Matrix or 3Design to build basic geometric bodies in 3D space according to the sketch, and gradually refines the ring arm, earring hook, inlay structure and decorative texture. Through the parametric function, key dimensions such as gem size, tolerance and wall thickness can be preset in the model, and adjusted and optimized in real time to ensure reasonable structure and aesthetic balance.
Model inspection and optimization
After the CAD design is completed, it is necessary to run the “Solid Analysis” and “Mesh Diagnosis” tools to check for potential problems such as thin walls, normal errors, overlapping faces and non-manifold geometry, and repair these defects. This link also includes setting a mesh tolerance of 0.01-0.02 mm when exporting the model to STL format, which not only retains surface details but also avoids subsequent jams caused by excessive file size.
CAM path planning and simulation
Import the optimized STL file into Mastercam, HyperMILL or other CAM software to generate roughing, semi-finishing and finishing tool paths in sequence. Through the simulation function of the software, focus on checking the tool motion trajectory, fixture interference and high-temperature areas during the cutting process. Engineers will set the cutting speed, feed rate and tool type for different materials (such as 18K gold, 925 silver, brass) to ensure both efficiency and safety.
First piece trial cutting and parameter fine-tuning
After exporting the final G-code, the operator performs the first piece trial cutting on the machine tool at a feed rate and speed of 30%–50%, and then immediately compares and measures key indicators such as wall thickness, tolerance, surface roughness, etc. If the deviation exceeds the design tolerance (usually ±0.02 mm), the engineer will return to the CAM software to fine-tune the cutting depth, step or feed speed, and record the best parameter combination to form a “golden parameter” library.
Batch production and quality control
After confirming that the first piece meets the design standards, it can be batch processed according to the “golden parameters”. During the production process, the project manager monitors the machine tool operation status and processing progress in real time through the ERP system, and regularly checks the finished products, focusing on checking the size consistency and surface finish. If necessary, the cutting strategy will be optimized again to ensure the overall output and quality stability.
Post-processing and assembly
After the batch processing is completed, it enters the post-processing links such as deburring, ultrasonic cleaning, polishing, electroplating or gold plating. Professional polishers will choose the appropriate polishing paste and grinding method according to different materials and textures to ensure a uniform and smooth finish. Finally, gemstone inlay and finished product assembly are carried out to ensure that each piece of jewelry meets the design expectations and passes strict quality inspection.

Benefits of CAD and 3D rendering for jewelry business
For jewelry companies and brand owners
Shorten product development cycle: Through CAD to achieve parametric design, designers can generate multiple styles in a few hours, combined with KeyShot or V-Ray real-time rendering, quickly obtain visualization effects, and save an average of 60% of time compared to traditional hand-painted and physical proofing.
Reduce sample costs: 3D rendering prototypes replace some physical proofing, saving wax molds, metal materials and labor processing costs, especially in high-end material projects (such as platinum, 18K gold), which can reduce sample costs by at least 20%.
Enhance brand image and market competitiveness: High-quality renderings and animated short films can be used on official websites, social media and e-commerce platforms to convey exquisite craftsmanship and high-end positioning, helping brands stand out in homogeneous competition.
For customers
Visual participation in design: Customers can instantly view rendering effects and make adjustments through online platforms. They can participate in the decision-making of design details (such as gem color, metal surface treatment) without going out or waiting for physical samples, thereby enhancing brand stickiness.
Enhance purchasing confidence: Realistic renderings and AR try-on experience allow customers to have an intuitive expectation of the shape, size and wearing effect of the final product, and the return and exchange rate is reduced by more than 30%.
Personalized customization experience: The rendering tool supports real-time switching of the same style in different materials and gem combinations. Customers can compare multiple options in a short time and get a pleasant process of exclusive customization.
What is the difference between jewelry rendering and finished jewelry?
Differences in light sources and scene settings
When rendering, D65 standard daylight or three-point photography lighting layout is often used to accurately simulate natural light and soft light effects; the actual finished product shooting is often affected by the indoor lighting of the shop, natural light, and the camera white balance adjustment, which makes the metal reflection intensity and color temperature in the photo have a deviation of 2%-5% from the rendering.
Material mapping and micro texture limitations
Even if a high-quality PBR material library is used, the performance of the rendering map in terms of reflectivity, normal details, and micro roughness depends on the sampling resolution; the actual jewelry surface will have subtle differences in texture and highlight distribution due to slight changes in polishing, brushing, or electroplating thickness.
Polishing and manual post-processing effects
During the polishing process of the real object, artificial factors such as polishing paste particles, grinding pressure, and tool angle will affect the final brightness and glossiness. Usually, the online rendering shows the theoretical optimal mirror effect, while the real object may have slight micro-textures or light spots due to manual operation, making the mirror reflectivity of the finished product slightly lower than the rendering expectation.
Managing customer expectations and proofreading processes
To reduce the gap, Fulcol will attach a “rendering and physical comparison guide” when delivering the rendering, and take photos of the physical object at the sample stage and display it side by side with the rendering. Through multi-angle comparison and light source description, customers can understand the range of differences between the rendering and the physical object, and make final confirmation before the final mass production to ensure the consistency of online and offline display.
Start Your Custom Order | Email: info@fulcol.com | Number: +86 13055603907 |
Working with Fulcol top jewelry manufacturers, the process from demand dialogue to delivery of finished products is clear and efficient. At the beginning of the project, you only need to submit a design brief (including style intention, material selection, budget and delivery time limit), and we will give a preliminary plan and quotation within 48 hours. After confirmation, the designer will quickly issue a CAD model and rendering effect diagram. During this process, you can make modifications at any time and we will update it in real time.
Fulcol has dual ISO 9001 and ISO 14001 certifications, and the entire process is transparent and traceable, ensuring that every piece of jewelry can accurately restore your creativity and meet high quality standards. Looking forward to working with you to let digital design and precision manufacturing inject unlimited possibilities into your jewelry brand.
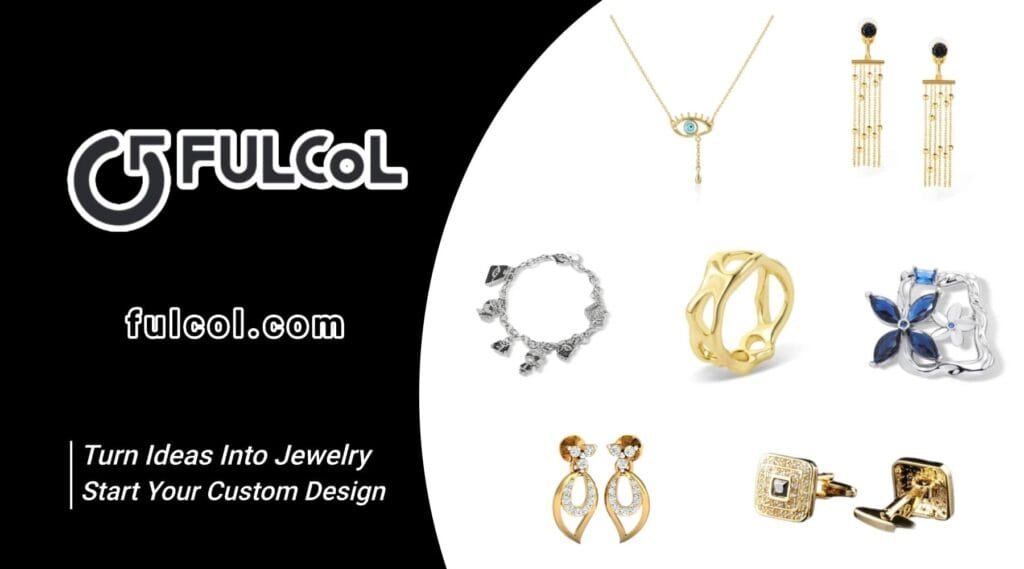