In the world of jewelry, the texture and luster of metal are often the first factors that attract people’s attention. All of this is inseparable from the key process of metal electroplating. From the 925 sterling silver rings worn daily to the luxurious and shining custom gem pendants, almost every piece of fine jewelry is made with the meticulous craftsmanship of electroplating technology.
In the field of jewelry design and production, electroplating is an extremely critical process. It not only determines the appearance, texture and color performance of jewelry, but also directly affects its durability, corrosion resistance and wearing comfort. For top jewelry manufacturers, exquisite electroplating technology can make ordinary materials instantly have the visual effect of high-end metals, and can also provide a broad creative space for personalized customization. For jewelry making wholesale suppliers of customized jewelry, the stability of the quality of the electroplating layer often determines whether the product can stand out in the market.
Taking Fulcol as an example, we have deeply realized in the long-term jewelry OEM process that electroplating is not only a decorative treatment, but also a sophisticated process that requires a high degree of technical accumulation and quality control. Fulcol will comprehensively analyze the professional knowledge of jewelry electroplating from multiple perspectives, including electroplating principles, process flow, material selection, characteristics of different metals, quality control, etc., to help manufacturers and wholesalers improve their competitiveness.
Table of contents
- Basic knowledge of metal electroplating: Principles that jewelry manufacturers must know
- Detailed explanation of electroplating process: introduction to process, materials and professional equipment
- Characteristics and applicable scenarios of different electroplated metals
- Electroplating quality control and common problem solutions
- Practical advice: How can jewelry manufacturers optimize electroplating quality?
Basic knowledge of metal electroplating: Principles that jewelry manufacturers must know
Metal electroplating (Electroplating) is a surface treatment process that deposits a layer of metal film on the surface of metal or other conductive materials through electrolytic reaction. This process is carried out through electrolytic chemical reaction. During electroplating, the jewelry is used as the cathode, the metal to be plated is used as the anode, and the target metal ions are dissolved in the electrolyte. When direct current is applied, the metal ions will be evenly deposited on the surface of the jewelry to form a dense and firm metal layer.
It can not only give the jewelry better color and visual effects, but also significantly enhance the product’s corrosion resistance, wear resistance and oxidation resistance. This process first appeared in the mid-19th century, but its application today has become highly sophisticated. The functions that can be achieved by electroplating include enhancing gloss, preventing oxidation, enhancing scratch resistance, and even changing the color of the product. For example, rhodium plating of silver can prevent silver jewelry from oxidizing and blackening, while gold plating enhances the sense of luxury.
Take sterling silver jewelry as an example. Although silver itself has a warm luster, it is easy to oxidize and turn black. By plating a layer of platinum or rhodium, it can not only prolong its beauty time, but also prevent silver from oxidizing and discoloring, thus improving the consumer experience.
In the field of jewelry, electroplating is often used for surface treatment of materials such as copper, brass, stainless steel, 925 silver, and alloys. This processing method is not only flexible in cost control, but also can quickly adjust product style and appearance according to market demand. It is currently one of the most flexible and commonly used surface treatment technologies.
In jewelry manufacturing, the quality of electroplating not only affects the appearance of the product, but also directly determines its service life and brand reputation.
Detailed explanation of electroplating process: introduction to process, materials and professional equipment
Although electroplating is a surface process, it is a systematic project. Negligence in any step may lead to problems such as peeling of the electroplating layer, uneven color, and insufficient gloss. The following is a standard metal electroplating process:
Pretreatment (degreasing and cleaning):
Before electroplating, the grease, oxide layer and impurities on the metal surface must be thoroughly removed. Common methods include ultrasonic cleaning, acid cleaning, alkaline cleaning, etc. This step is critical. If the cleaning is not thorough, the electroplating layer will not adhere firmly.
Pickling or activation:
Use dilute acid to activate the metal surface to enhance the adsorption capacity of metal ions and help the uniform deposition of subsequent metal layers.
Bottom layer electroplating (such as copper plating)
Before precious metal electroplating, a layer of copper is usually plated as an intermediate layer to enhance adhesion and uniformity. Sometimes a layer of nickel is added to enhance corrosion resistance.
Main plating (gold, silver, rhodium, etc.):
Select the final metal layer to be displayed according to the design and needs, and accurately adjust the thickness and gloss by controlling parameters such as current density, temperature, time, and stirring speed.
Rinse and neutralize:
Remove chemicals remaining during the electroplating process to avoid metal corrosion or surface defects.
Drying and inspection:
Use a hot air drying oven for thorough drying, and finally the quality inspector will visually and instrumentally inspect the electroplating effect.
The professional equipment required for electroplating includes DC power supply, electroplating tank, constant temperature heating device, stirring system, anode suspension rack, etc. High-quality equipment can significantly improve the uniformity and stability of the coating and reduce quality fluctuations caused by human intervention.
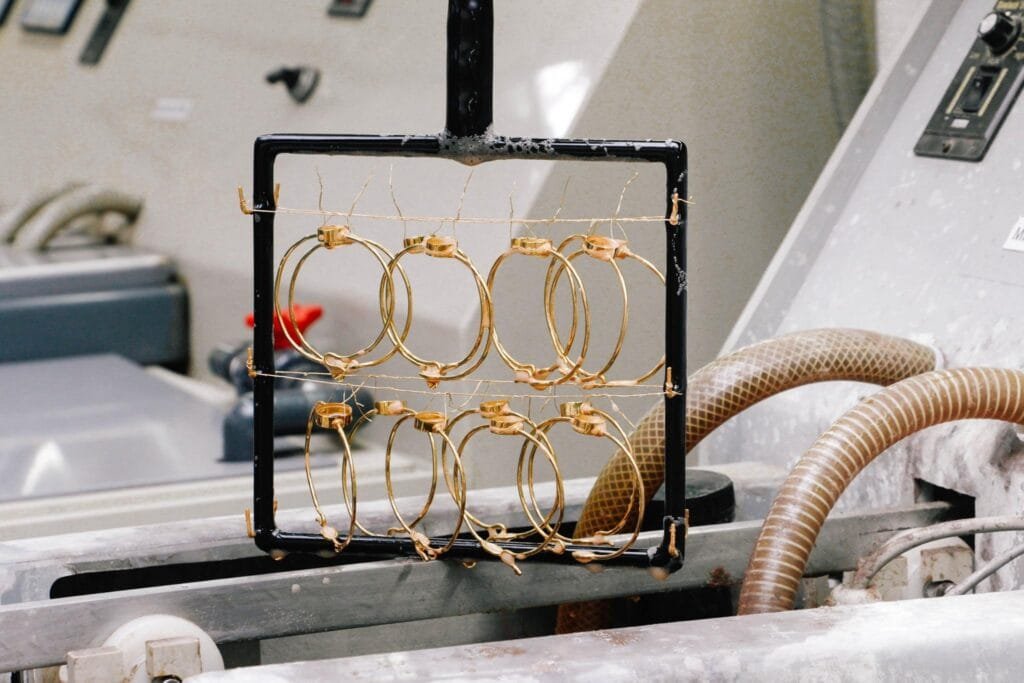
Characteristics and applicable scenarios of different electroplated metals
The electroplated metals commonly used in jewelry have their own characteristics. Different metals have different visual effects, wear resistance and application directions. Understanding these differences will help jewelry manufacturers make more targeted choices during the design stage.
Gold electroplating
Gold electroplating is the most widely used electroplating method in jewelry. It is widely used in high-end jewelry because of its warm color and luxurious feel. It is not only limited to decorative purposes, but also reflects the grade of the product.
Common 18K and 24K tones have good oxidation resistance. Note that the pure gold layer is soft and should not be too thick. It is generally controlled at 0.1~0.3 microns. According to color, it can be divided into gold electroplating, rose gold electroplating, etc. Its advantages are:
- Rich and elegant, stable color.
- The chemical properties of the metal are stable and not easy to oxidize and discolor.
- Strong compatibility with most gemstone colors.
The disadvantage is that if the plating is too thin, it may gradually fade due to friction during wearing. The thickness of the plating needs to be controlled and a protective layer is recommended.
Silver plating
Silver plating is used for low-cost imitation metal jewelry or for covering other metals with a layer of silver to enhance the surface gloss and skin-friendly feel due to its bright reflective effect. However, silver is easy to oxidize and will turn black without special treatment. Therefore, many jewelry will be first silver-plated and then a layer of rhodium protective layer will be added.
Rhodium plating
Rhodium is a rare and precious metal that is expensive and is usually used as a surface treatment for high-end jewelry. It has extremely high gloss and excellent corrosion resistance. In high-end silver jewelry and electroplated platinum jewelry, rhodium is often used for electroplating. Its advantages include:
- White color and high reflectivity give the jewelry a mirror-like gloss.
- Strong antioxidant properties can keep the product from changing color for a long time.
- Gentle to the skin, low risk of allergies.
However, rhodium is expensive, and the plating thickness is usually 0.1~0.3 microns. If the process control is not good, it is easy to fall off, so the factory’s electroplating control technology is required to be high.
Nickel and palladium electroplating
Nickel is often used as an intermediate plating layer to enhance adhesion and corrosion resistance. However, since some people are allergic to nickel, nickel-free electroplating is required for exports to Europe and the United States. Palladium is the first choice for the intermediate plating of gold electroplating. It is not only safe, but also can improve the color stability.
Black Rhodium or Black Gold Electroplating
In recent years, the popular dark style jewelry mostly uses black rhodium electroplating, which gives the jewelry a cool and personalized style, but the stability of black rhodium is slightly lower than that of ordinary rhodium, and it is easy to fade slightly during wearing, so it is more suitable for jewelry rather than high-frequency jewelry.
Electroplating quality control and common problem solutions
In jewelry production, electroplating quality directly determines customer satisfaction and repurchase rate. The following are some common electroplating problems and corresponding solutions.
Uneven electroplating
The causes usually include uneven current distribution, poor plating solution stirring, and incorrect workpiece placement. The solution is to adjust the electrode spacing, use a rotary stirring system, or correct the hanger design.
Surface blistering or roughness
Mostly caused by insufficient pretreatment or excessive current, the cleaning steps should be strengthened, and the electroplating parameters should be optimized, such as reducing the current density or shortening the electroplating time.
Plating shedding
This is usually related to the pretreatment process or the compatibility of the underlying metal. The metal bonding can be improved by increasing the type of pre-plating and extending the activation time.
Uneven plating or color difference
Common in gold or rose gold plating. It is necessary to ensure that the plating solution concentration is balanced and the temperature is constant, and the electrolyte is replaced regularly to maintain the composition ratio.
In Fulcol’s actual case, we used an automatic constant temperature system and an intelligent current control module to successfully increase the rose gold plating pass rate to more than 98%, effectively ensuring the consistency of batch product quality.
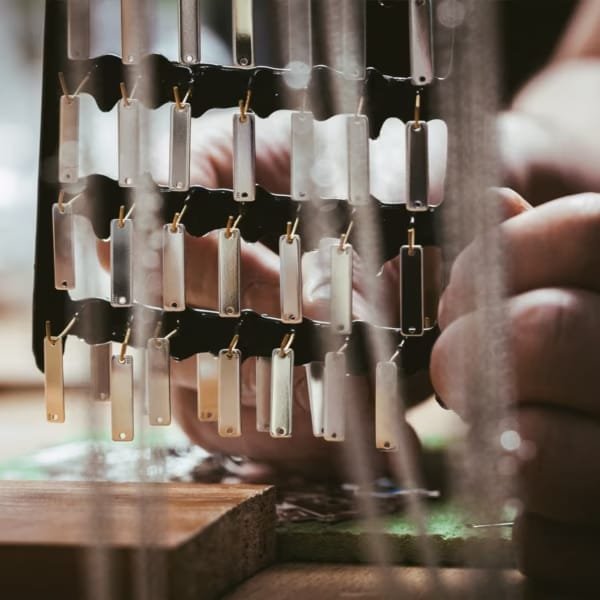
Practical advice: How can jewelry manufacturers optimize electroplating quality?
For jewelry manufacturers and custom jewelry wholesale suppliers, optimizing the electroplating process and ensuring the stability of the finished product is a key step in building brand reputation. The following suggestions are for reference:
Choose the right electroplating materials and ratios
Jewelry of different materials and different uses should choose the right electroplated metal. For example: daily rings should give priority to the wear-resistant rhodium plating, while custom brooches for display can consider the highly reflective electroplated gold layer.
Control the electroplating thickness
Usually, the thickness of jewelry electroplating should be controlled between 0.1 and 2.5 microns, depending on the specific usage scenario. Too thin is easy to wear, too thick will affect the details and cost.
Finely test each batch of products
It is recommended to introduce X-Ray coating detectors for non-destructive testing to ensure that the thickness and quality of each batch of electroplating meet the standards.
Focus on employee skill training and operating standards
Electroplating operators need to undergo professional training and master the details of different electroplating solution ratios, current regulation, electrolytic cell temperature control and other management capabilities.
Establish a stable electroplating supply chain system
Working with experienced electroplating processing partners or building a standardized electroplating workshop in-house can help unify process standards and improve production efficiency.
Start Your Custom Order | Email: info@fulcol.com | Number: +86 13055603907 |
Metal electroplating is not just a physical process, it is a bridge between design creativity and consumer experience. High-quality electroplating can make ordinary materials shine with precious brilliance, while poor electroplating will quickly damage the brand image.
In-depth understanding of the principles and practical details of electroplating is the only way to enhance product added value and differentiated competitiveness. In this industry where details determine success or failure, electroplating not only determines the beauty of jewelry at first glance, but also determines whether consumers are willing to choose your products again.
With rich experience in metal electroplating, Fulcol continues to provide global customers with jewelry customization services that combine creativity and quality. We believe that real jewelry is not only about its material and luster, but also about whether it can stand the test of time. Choosing high-quality electroplating is choosing a more competitive future.
Starting from the overall perspective, assist in optimizing design, proofing, quality inspection and other links to jointly create replicable and high-standard electroplating solutions.
If you need more information about customized metal electroplating solutions or technical consultation, please contact our technical team and we will tailor the most suitable electroplating solution for you.
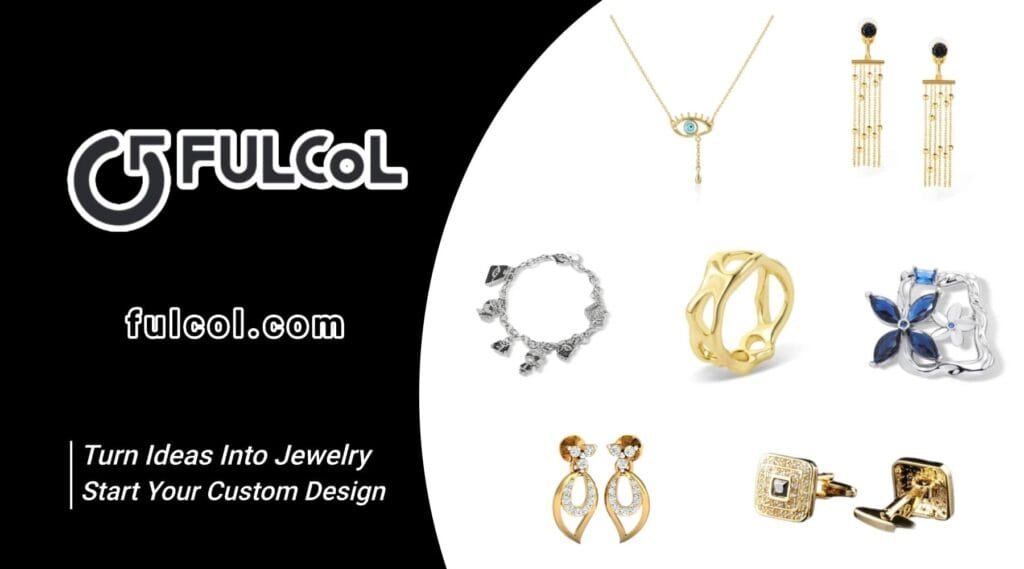